Flower vending machines offer a convenient and accessible way for people to purchase fresh flowers on the go. However, to ensure the flowers remain vibrant and appealing, careful attention to maintenance and quality control is crucial. From monitoring refrigeration systems to tracking flower freshness, managing these machines involves a blend of technology and hands-on care. Here’s an in-depth look at the essential aspects of maintaining flower vending machines and ensuring the quality of the flowers they dispense.
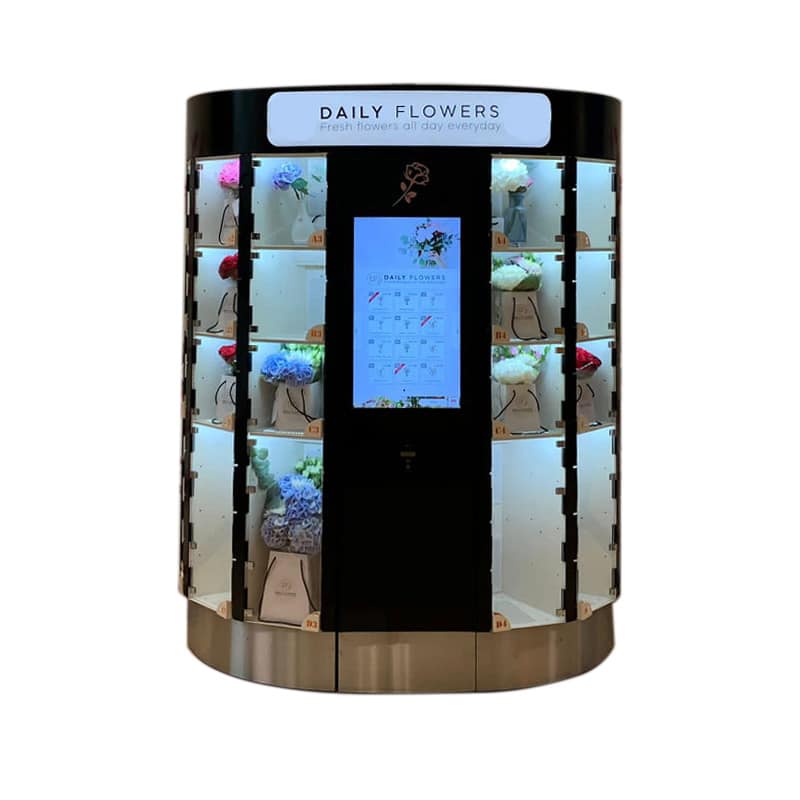
1. Regular Temperature Control Checks
One of the most important aspects of flower vending machine maintenance is temperature control. Flowers are delicate and require specific cool temperatures to stay fresh and avoid premature wilting. Many flower vending machines are equipped with refrigeration systems to maintain an optimal temperature range. Regular checks on these refrigeration systems help ensure that flowers are stored at a consistent temperature, preserving their quality. Any deviation from the ideal range can lead to flower spoilage, so routine inspections and temperature monitoring are essential.
2. Monitoring Humidity Levels
Flowers also require a certain level of humidity to maintain freshness. While high humidity can lead to mold growth, low humidity may cause flowers to dry out prematurely. Modern flower vending machines come with built-in humidity control features, allowing operators to keep flowers at an ideal moisture level. Regular calibration and maintenance of these systems help maintain a delicate balance, ensuring flowers are neither too dry nor overly humid.
3. Frequent Stock Rotation
Flowers in vending machines need to be rotated regularly to maintain freshness and quality. Older flowers must be removed before they reach the end of their lifespan, making room for fresh stock. Stock rotation schedules are often organized around the natural lifespan of each flower type, with some flowers needing replacement sooner than others. This systematic rotation helps ensure customers receive high-quality, fresh bouquets every time they purchase from the machine.
4. Cleaning and Sanitizing the Machine
To prevent bacterial growth, odor, and general grime buildup, flower vending machines must be cleaned and sanitized regularly. This includes wiping down interior surfaces, disinfecting flower holders, and ensuring no water leaks that could lead to mold or mildew. Regular cleaning not only keeps the machine looking attractive but also prevents contamination that could affect flower quality. A routine cleaning schedule is crucial for maintaining both hygiene and appearance.
5. Inspection and Replacement of Packaging Materials
Most flower vending machines provide flowers in protective packaging, which may include wrappers, stems, and water capsules. Over time, packaging materials can deteriorate, losing their effectiveness at keeping flowers hydrated or protected. Regular inspection of these materials ensures that each bouquet is delivered in pristine condition. Damaged or worn-out packaging should be replaced promptly to maintain the presentation quality and ensure flowers reach customers in optimal condition.
6. Preventative Maintenance of Mechanical Parts
Flower vending machines rely on several moving parts, including dispensers, trays, and payment processing systems. Regular maintenance of these mechanical components prevents unexpected breakdowns and ensures the smooth operation of the machine. Technicians should conduct routine inspections and apply preventive measures, such as lubricating parts and checking for loose components. Addressing these issues proactively keeps the machine reliable and minimizes downtime, which could impact sales and customer satisfaction.
7. Real-Time Quality Monitoring Systems
To ensure continuous quality, some flower vending machines are equipped with real-time monitoring systems that track temperature, humidity, and flower freshness. These sensors can alert operators when conditions deviate from the ideal range or when flowers need to be replaced. With real-time updates, operators can address potential issues before they impact the customer experience. This technology also allows for remote monitoring, making it possible to manage multiple machines efficiently across different locations.
8. Inventory and Supply Chain Management
Proper inventory management is crucial for flower vending machine operators to keep up with demand and avoid overstocking or understocking. A well-organized supply chain ensures that fresh flowers are delivered and restocked in a timely manner, preventing spoilage. Many operators use inventory tracking software to monitor stock levels and plan restocking schedules according to the sales pace. Reliable suppliers who can provide fresh flowers on schedule are also critical for maintaining quality control.
9. Regular Testing and Calibration of Sensors
Sensors are responsible for tracking internal conditions, including temperature, humidity, and flower freshness. However, sensors can drift out of calibration over time, leading to inaccurate readings that may compromise flower quality. Routine calibration ensures that sensors provide reliable data, allowing operators to make informed maintenance decisions. Regular testing of these sensors helps maintain an accurate picture of machine conditions and prevents unexpected quality issues.
10. Customer Feedback Collection and Analysis
Customer feedback is a valuable tool for assessing the performance and quality of flower vending machines. Operators can encourage customers to share their experiences, noting any issues with flower quality, packaging, or machine functionality. Feedback can be collected through QR codes on receipts, customer service contact information, or a dedicated website. Analyzing this feedback helps identify trends or recurring issues, allowing operators to make improvements and prioritize maintenance based on customer experiences.
11. Rapid Response to Technical Malfunctions
Technical malfunctions, such as payment issues or dispensing errors, can cause frustration for customers. To avoid negative experiences, vending machine operators should have a rapid response system in place. This may include remote diagnostics, on-call technicians, and customer service contacts that customers can reach out to if an issue arises. Addressing malfunctions quickly not only maintains customer trust but also minimizes downtime, keeping the machine operational and reliable.
12. Ensuring Sustainability and Eco-Friendly Practices
Maintaining sustainability in flower vending machines includes using recyclable or biodegradable packaging and eco-friendly refrigeration systems. Regular evaluation of environmental practices and replacement of non-sustainable materials with eco-friendly options are crucial for meeting modern environmental standards. This commitment to sustainability also resonates with customers, who are increasingly looking for green options even in automated retail settings.
Maintenance and Quality Control
Maintenance and quality control are essential to the success of flower vending machines, directly impacting customer satisfaction and operational efficiency. From temperature and humidity regulation to customer feedback analysis and quick response to technical issues, every aspect of maintenance ensures that customers receive fresh, high-quality flowers every time. With robust quality control practices and regular upkeep, flower vending machines can deliver an exceptional floral experience, bringing beauty and convenience to urban spaces, events, and everyday settings. As these machines become more advanced, effective maintenance and quality control will continue to play a pivotal role in their success, supporting the industry’s growth and enhancing the experience for flower lovers everywhere.